Lotus Suspension Analysis
Lotus Suspension Analysis 5.03 Crack 0 Comments According to several large European distributors, in the nearest future is to launch sales of its Special Edition Xbox with the original semi-transparent design — The Xbox Crystal Pack. To improve search results for Lotus Suspension Analysis 5.0 try to exclude using words such as: serial, code, keygen, hacked, patch, warez, etc. Simplifying your search query should return more download results. Many downloads like Lotus Suspension Analysis 5.0 may also include a crack, serial number, unlock code or keygen (key generator). Lotus Suspension Analysis 5.0 Information Lotus Suspension Analysis 5.0 was added to DownloadKeeper this week and last updated on 25-Nov-2020. New downloads are added to the member section daily and we now have 424,265 downloads for our members, including: TV, Movies, Software, Games, Music and More.
Michael Cattani – michael.cattani@raceup.it
Introduction
The topic of this project is the kinematic analysis of an independent suspension, taking into consideration the suspension system of the Formula SAE electric car of the University of Padua (RaceUP Team).
The project started from the knowledge of the kinematic points of the car (year 2017/18), and then created a model for the analysis of all the parameters influencing the dynamics of the vehicle like Toe, Camber, Kingpin angle and more. Once the model was finished I tried to optimize the system through the DOE of Adams View
Objectives
First of all I developed the model in Adams View, then I checked if the output results were correct. To verify that, I compered my results with the results obtained using Lotus Suspension Analysis Software. Since the results were the same and my model was correct, I decided to use this model. Initially the model had 2 actuators that raised and lowered the wheels (with a static frame). This configuration was correct for bump and rebound, but not when I simulated rolling. So I modified the model by importing the frame, moving it while the wheels were on the ground.
Then I used this model for the optimization of the kinematics points. Using DOE in Adams with many parameters and level of measures is very difficult (too many eperiments required), so I dealt with the problem by looking for the main parameter and optimizing this one. Then I checked that the others parameters were correct.
The modelling problem
The origin of the car’s reference frame is fixed to the projection on the ground of the furthest poin of the frame, while the axes are oriented as: X coincides with the longitudinal direction of the vehicle (pointing to the rear of the car) and Y axis points to the right of the car, Z axis points upward. Adams settings: MMKS, gravity along Z downward.
Front Right Points:
Point Name | X | Y | Z | Description |
WUF | 288.374 | 242.242 | 88.758 | Upper wishbone front pivot |
WUR | 554.028 | 265.204 | 286.361 | Upper wishbone rear pivot |
WLF | 407.868 | 211.676 | 127.155 | Lower wishbone front pivot |
WLR | 599.414 | 244.272 | 144.446 | Lower wishbone rear pivot |
Toe_Frame | 334 | 225 | 140 | Toe Arm Inner joint |
Frame_Damper | 459.7 | 58.9 | 570.1 | Spring to damper support pivot |
Upper_Joint | 455 | 500 | 325 | Upper wishbone outer ball joint |
Lower_Joint | 444 | 550 | 138 | Lower wishbone outer ball joint |
Toe_Upright | 398 | 558 | 157.5 | Toe Arm outer ball joint |
Wheel_Centre | 445 | 613 | 228.99 | |
Wheel_Axes | 445 | 413.01 | 227.25 | |
Push_Joint | 453.551 | 471.588 | 337 | Upper Wishbone to Pushrod pivot |
Contact_Ground | 445 | 615 | 0 | Wheel contact |
Rack_Centre | 334.0 | 0 | 140 | Centre of the rack |
Rocker_Damper | 459.7 | 225.954 | 622.235 | Rocker-Spring joint |
Push_Rocker | 459.7 | 290.446 | 577.217 | Rocker-Pushrod joint |
Rocker_Support | 459.7 | 230.5 | 552.408 | Rocker Centre of rotation |
Rocker_Axes | 449.7 | 230.5 | 552.408 | Rocker axes |
The front left points are the same of the previous ones, with a negative Y coordinate.
Step up full movie download in hindi. Bodies and Joints:
The created model has various bodies: Frame, Rack, Wheel (FR, FL), Wheel Group (FR,FL), Pushrod (FR,FL), Rocker (FR,FL), Upper Wishbone (FR,FL), Lower Wishbone (FR,FL). These bodies contain both the points in the precendet table and the elements imported from CATIA. The elements were imported in .stl format due to problems with the CAD software in student version.
Joint:
– Revolute joint in WUR with the rotation axis pointing through WUF between Upper Wishbone and Frame
Lotus Suspension Analysis Pdf
– Revolute joint in WLR with the rotation axis pointing through WLF between Lower Wishbone and Frame
– Spherical joint in Upper_Joints between Upper Wishbone and Wheel Group
– Spherical joint in Lower_Joints between Lower Wishbone and Wheel Group
– Spherical joint in Toe_Upright between Toe arm and Wheel Group
– Spherical joint in Pushrod_Joint between Upper Wishbone and Pushrod.
– Revolute joint in Wheel_Centre between Wheel and Wheel_Group.
– Revolute joint in Rocker_Support with the rotation axis pointing through Rocker Axes between Rocker and Frame
– Hooke joint in Push_Rocker between Pushrod and Rocker
– Hooke joint in Toe_Frame between Toe Arm and Rack
– Translate Joint in Rack Centre between Rack and Frame
– Inplane Joint in Contact_Ground between Wheel and Ground
– Translate Joint or Revolute Joint in the car Centre of Mass, between Frame and Ground
Motion:
– Rotational Joint motion on the revolute joint between wheel and wheel group. In this model is set equal to 0, but it’s important for a future upgrade of the model
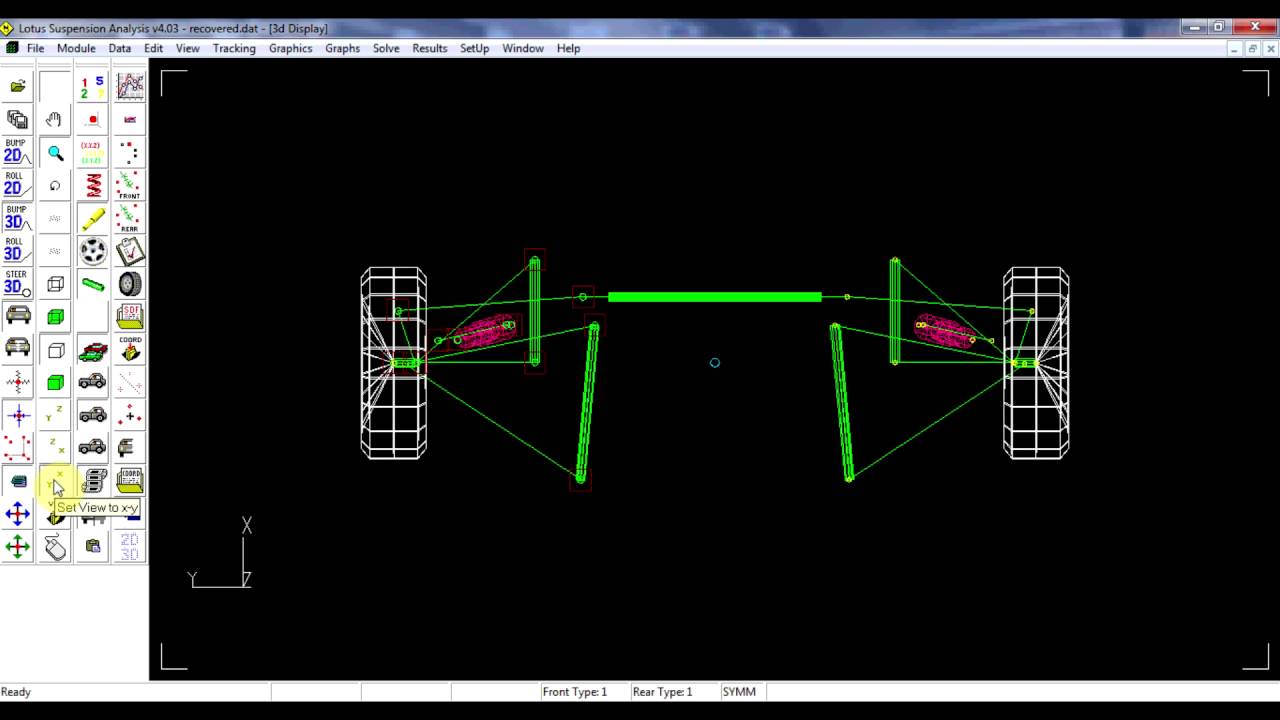
– Translate Joint motion or Rotational Joint motion in the joint between Frame and Ground. It’s important because this motion simulate the car move in bump/rebound and during the rolling. The translate motion is set between +35/-35 mm while the roll is set between +2/-2 deg
– Translate Joint motion in the joint between Frame and Rack. It’s important because this motion simulate the car during the steering; the steering is set between +30/-30mm
At the end the Gruebler count is:
This is the result of what I have done up to this point:
1) Simulate the cornering of the car –> Roll
2) Simulate the motion of the suspension –> Bump_Rebound
3) Simulate the steering –>
Main Parameters of the Model:
In order to have a perfect control, I created a point called “MeasurePoint” that is on the rotational axes of the wheel and has a specific distance from the wheel center. With a Point to Point Measure between these 2 point I can get the X Y and Z displacement during the entire simulation.
Toe: atan2(ΔX,ΔY)*180/π , toe will be positive when is toe in, and negative when is toe out; Free xilisoft video converter ultimate license code.
Camber: atan2(ΔZ , sqrt(ΔX^2+ΔY^2))*180/π , if the bottom of the wheel is farther out than the top, it is called negative camber;
For the KPI and Caster angle, I introduced other Point to Point measures (X,Y,Z) between Lower and Upper Joint. So, I got ΔX_LJ-UJ, ΔY_LJ-UJ and ΔZ_LJ-UJ
Kingpin Incination (KPI): 90-atan2(ΔZ_LJ-UJ , ΔY_LJ-UJ)*180/π , positive the Lower Joint in further then Upper Joint (plane YZ)
Caster angle (CA): 90-atan2(ΔZ_LJ-UJ , ΔX_LJ-UJ)*180/π , positive when the Lower Joint in further then Upper Joint (plane XZ)
For the Scrub Radius and the Mechanical Trail, I introduce 2 other important point: 1)the point obtained as an intersection between the kingpin axis and the ground; 2) the point obtained as an intersection between the wheel axis and the ground.
Roll Center High
Simulations and analysis of results
First Simulation (2017/18 Kinematic points)
Lotus Suspension Analysis
Consider only the right wheel, for the left one I can use the symmetry:
Lotus Suspension Analysis Price
Bump&Rebound
Roll (positive when cornering to the right)
Steer (positive when steering to the left)
Through these results we can see that the Toe is too variable, both in bump / rebound and rolling. This is not positive because during the run the driver could “feel” variations in the behavior of the car. Invece, la curva del recupero camber è adeguata per la FSAE. Values such as roll center height, mechanical trail and radius scrub must remain constant, being very important for vehicle stability.
OPTIMIZATION:
Lotus Suspension Analysis Crack
As mentioned above, I focused on optimizing toe, trying to minimize its variation as much as possible. First of all I decided the parameters that could be changed, trying (first try) not to change the kinematic points to the frame (they would involve the remaking of new parts).
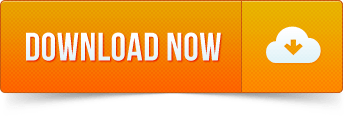